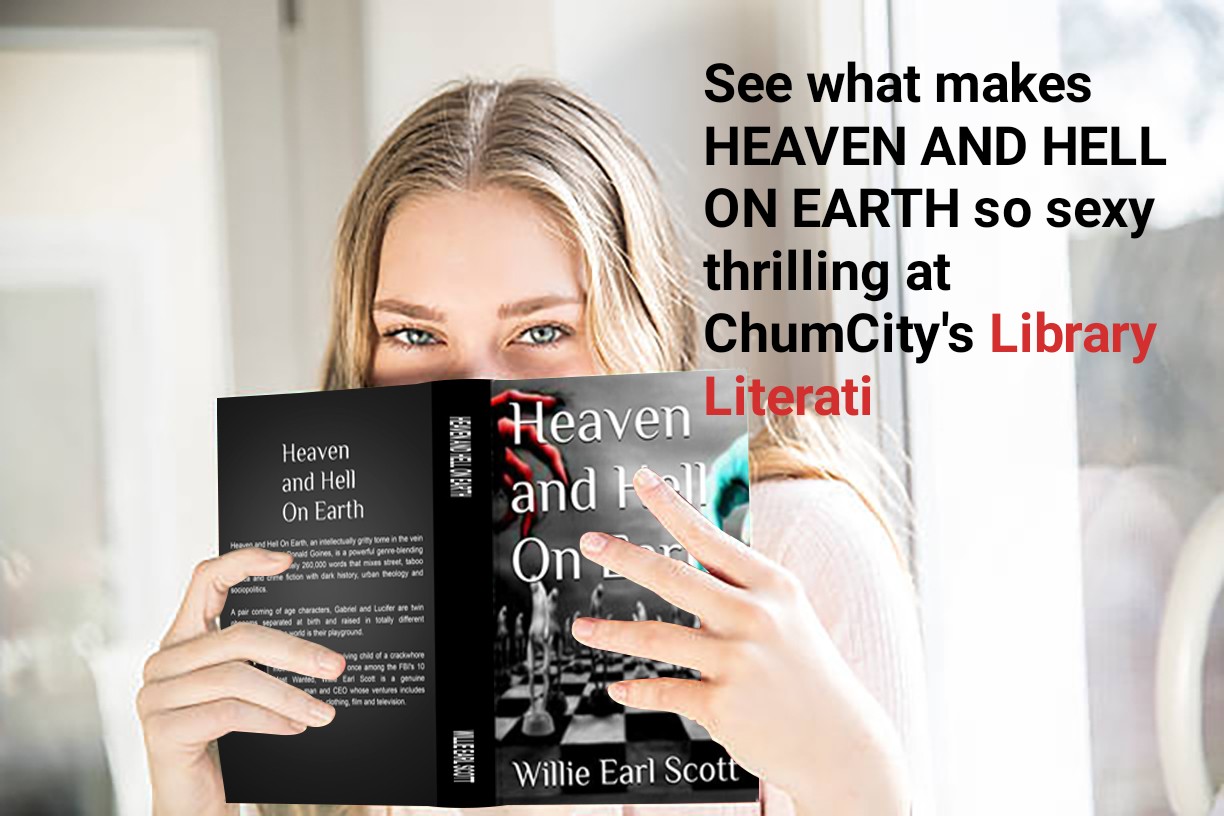
Photo courtesy DepositPhotos.

Facing an uncertain economy and rising interest rates, companies of all sizes are trying to cut costs. An increasing number are using technology to improve and secure their operations, but the boost they get may be limited unless their underlying processes are up to speed. That is where Business Process Engineering (BPE) can help.
Assisted by an experienced outsourced IT support partner, a BPE review can identify time-consuming bottlenecks and other obstacles. Such a review can also suggest new, streamlined approaches that can cut unnecessary expenses and deliver dramatic improvements in productivity, cycle times, and quality.
At its core, a Business Process Engineering engagement aims to cut down enterprise costs and process redundancies; and trained BPE professionals will comprehensively reassess an organization’s structure and workflow, recommending ways to enhance value at each step of manufacturing, paperwork, or other processes, accelerating information flows while eliminating errors and rework. A partner expert will also objectively review and document existing systems and procedures and suggest improvements that will save time and money.
A Business Process Engineering review can also improve the performance of crucial operations by recommending ways to reduce costs and cycle times, eliminating unproductive activities, reorganizing teams to decrease management layers, and identifying unnecessary handoffs that add time and cost to activities. Although the specific steps of the process may differ, depending on an organization’s individual circumstances, most Business Process
Engineering engagements include these stages:
Mapping the current state of the client’s business processes
During this initial benchmark phase, the BPE lead will gather data from the client’s digital and other resources to gain a detailed understanding of how the process is currently performing.
- Analyzing processes to identify gaps, disconnects, bottlenecks, and other inefficiencies.
In this phase, a BPE analyst will investigate and identify errors and delays that impede efficient process flows. The analyst will also document their findings.
- Identifying improvement opportunities.
During this “thousand-foot overview,” the BPE professional will document and review existing steps in a client’s processes and determine which ones are necessary. Some processes may be streamlined by replacing manual tasks with automation.
- Designing a map for the future.
The BPE analyst will create and document new processes to solve bottlenecks and other challenges identified during the engagement and design KPIs, or key performance indicators, for every step. Findings will be presented in an easy-to-understand graphic format that management can use to add efficiency and reduce expenses across departments and functions.
- Working with the client to implement improvements.
The BPE consultant will communicate with appropriate stakeholders to implement new processes, ensure their familiarity with necessary activities, and design and schedule monitoring initiatives to periodically review the application of the new processes and modify them if needed.
Standardizing and automating workflows to reduce errors and fragmentation while establishing clear ownership of processes can reduce business costs and cycle times by eliminating unproductive activities and establishing an efficient and effective environment. An in-depth Business Process Engineering engagement can help organizations improve their overall quality metrics, reduce errors and enable employees to focus on higher-value activities while shrinking workflow fragmentation.
Carl Mazzanti is president of eMazzanti Technologies in Hoboken, N.J., providing IT consulting services for businesses ranging from home offices to multinational corporations.
e